Project of the Year: Industrial Category
Strengthening of a Reinforced Concrete Preheater Tower
Florence, Colorado
Submitted by Construction Technology Laboratories, Inc.
Owner
Holcim (U.S.) Inc.
Florence, Colorado
Project Engineers/
Designers
Construction Technology Laboratories, Inc.
Skokie, Illinois
Walker Restoration Consultants
Greenwood Village, Colorado
Holcim Group Support (Canada), Ltd.
Mississauga, Ontario, Canada
Repair Contractor
Structural Preservation Systems, Inc.
Baltimore, Maryland
Material Suppliers
VSL
Hanover, Maryland
Sika Corporation
Lyndhurst, New Jersey
Inspection by plant personnel revealed cracking in the concrete frame of a 326-ft-tall, 7-level preheater tower. On-site plant engineers deemed the cracking significant, as the structure supports critical manufacturing process equipment. A structural engineering consulting firm was retained to evaluate the extent of the problem and formulate a repair plan. The firm mobilized at the site in less than 24 hours and performed an initial structural safety assessment. A comprehensive structural evaluation indicated that the structure required strengthening.
Restoration consultants were engaged to assist locally with engineering and construction administration. A specialty repair contractor also was engaged to review the constructibility of several alternate repair schemes and maintain the fast-track schedule.
After considering structural capacity and serviceability requirements, durability issues, the high-temperature operating environment, constructibility, and an aggressive construction schedule, the team recommended a retrofit consisting of bonded post-tensioning within internal holes drilled in the beams. This solution was quite extraordinary, as it required precision-drilling horizontal holes up to 87 ft long in the beams of the elevated frame structure, without cutting existing embedded reinforcement.
Nondestructive impulse radar testing was used to locate existing embedded reinforcing steel, as well as to monitor the drilled holes’ trajectory. This process helped ensure proper tendon alignment and prevent damage to embedded steel. The cored holes served as post-tensioning ducts.
The repairs were executed quickly and under challenging circumstances, including working high on the exposed structure through a cold winter with severe wind conditions. The unique retrofit resulted in a structure that is stronger, more serviceable, and more durable than the original tower.
Award of Excellence
Eden Roc Hotel
Award of Excellence: High-Rise Category
Eden Roc Hotel
Miami Beach, Florida
Submitted by BASF Building Systems
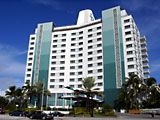
Owner
Capital Hotel Management
Beverly, Massachusetts
Project Engineer/
Designer
Tadjer-Cohen-Edelson Associates, Inc.
Silver Spring, Maryland
Repair Contractors
C.A. Lindman, Inc.
Pompano Beach, Florid
Balvac
East Aurora, New York
Material Supplier
Fox Industries
Baltimore, Maryland
The two ceramic-tiled, 30 ft wide by 140 ft tall towers framing the front elevation of the Eden Roc hotel in Miami, Florida, had become debonded. A preliminary evaluation by others indicated massive debonding with a severe potential of fall from the building. There appeared to be only one solution: complete removal and replacement with a cost of over $1,600,000 and many months of disruptive reconstruction.
Engineers performed a detailed evaluation using Impact Echo supplemented with core extractions to determine the viability of an alternate method of repair. Due to the influence of the historic South Beach district surrounding the hotel, a nondestructive method of reestablishing the bond and structural integrity was essential. Conventional epoxy injection was considered, however, the pressure of the injection process could have pushed the tile further away. Gravity feed epoxy injection would not have adequate coverage. Thus, a combination of vacuum injection enhanced with direct pinning was evaluated.
The design proposed by the engineers reestablishes structural integrity of both the tile and the grout by pinning the tile/grout component to the backup CMU component and filling all voids with a Portland cement enriched methylmethacrylate (MMA). Pins were placed throughout the entire facade at 24 in. spacing and ports were inserted into 3/8 in. holes which served as both a vacuum exit and an entry to introduce the MMA.
With the completion of the tile repair and restoration, full structural integrity has been restored. The walls were retested with Impact Echo to verify establishment of full contact, all of which was completed at a cost of $550,000—less than half the cost of the originally proposed removal and replacement!
Jefferson Davis Monument Restoration
Award of Excellence: Historic Category
Jefferson Davis Monument Restoration
Fairview, Kentucky
Submitted by Wiss, Janney, Elstner Associates, Inc.
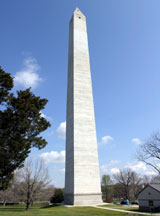
Owner
Commonwealth of Kentucky
Department of Parks
Frankfort, Kentucky
Project Engineer/
Designer
Senler, Campbell
Associates, Inc.
Louisville, Kentucky
Repair Contractor
Mid-Continental
Restoration, Inc.
Fort Scott, Kansas
Concrete Consultant
Wiss, Janney, Elstner Associates, Inc.
Chicago, Illinois
The Jefferson Davis Monument was built between 1917 and 1924 in Fairview, Kentucky. The monument is approximately 351 ft tall and was constructed as an unreinforced concrete obelisk with walls 7 ft, 8 in. thick at the base and 2 ft thick at the top. The monument walls were constructed with a base mix placed in two foot lifts with a formboard finish, covered with a one inch thick white cement face mix. Deterioration of the unreinforced concrete was caused by cyclic freezing and thawing of saturated concrete.
The rehabilitation project was prompted by the continuing deterioration of the exterior facade and the safety hazard posed by falling concrete. The goal of the rehabilitation project was to repair the exterior concrete and reduce the rate of future deterioration. The primary objective of the repairs was to use materials and techniques that would be sympathetic to the existing facade, match the original concrete, and perform well.
The repair work was performed in two phases that included use of different types of access due to budget and schedule requirements. The repair work in Phase 1, at the top of the monument, used swingstage scaffold supported by a steel bracket. The work in Phase 2, at the lower portion of the monument, used ground supported pipe scaffold with work platforms.
The project included developing sample repair materials and procedures to match the original appearance. At least fifty, one by one ft samples were prepared using different proportions of grey and white cement and aggregate components, various forming techniques, and different finishing techniques. One of the most difficult challenges involved creating inconsistencies in the formwork to reproduce the varied appearance of the original concrete. Concrete repair materials were placed using form and pour techniques, and were anchored to the original base mix concrete by embedded dowels.
During the sample and trial repair phases of the monument rehabilitation, procedures and materials were developed and adjusted to achieve a concrete repair that matched the adjacent original concrete. An important aspect of this project, as with any historic repair work, was the planned implementation of a review and approval process as part of the project.
Coral World Ocean Park
Award of Excellence: Longevity Category
Coral World Ocean Park
St. Thomas, U.S. Virgin Islands
Submitted by Matcor, Inc.
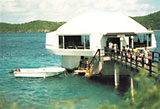
Owner
Coral World Ocean Park
St. Thomas, U.S. Virgin Islands
Project Engineer/
Designer
Matcor, Inc.
Doylestown, Pennsylvania
Repair Contractor
Matcor, Inc.
Doylestown, Pennsylvania
The Coral World reinforced concrete, underwater observation tower sits in the ocean, subjected to the salt-laden trade winds. The structure was built in stages using salt contaminated sand and water. Over time, the reinforcing steel severely corroded and cracked the concrete. The structure underwent one major conventional repair. Corrosion continued and major cracks/spalls reappeared. The owners and their engineers decided that a permanent solution was required. A cathodic protection (CP) company was chosen to provide a CP system for the structure. Except for the roof, the entire structure is reinforced concrete. The system had to be easy to install on all surfaces and easy to maintain. A conductive coating system was chosen. Except for a few cable connections to the reinforcing steel and the placement of reference electrodes, the entire system was placed on the surface of the concrete. The cables and control wires ran to the existing control room and terminated at the CP controller.
The severest damage was on the radial beams. The owner’s structural engineering firm specified the spalled concrete be removed, a new epoxy coated reinforcing steel cage placed over the beam, and new concrete poured. This was difficult—some beams were over water and the reef tank had to be sectioned, the fish removed, and the tank drained.
Much of the exposed steel was badly corroded and not electrically continuous. The original steel was extensive, and additional steel was not required. A series of electrical bonds was necessary for the CP system.
With repairs made and instrumentation in the concrete, the surfaces were covered with the conductive coating. The CP company’s platinum anodes were placed on the surface with special, self-adhesive fiberglass tape. A second coat of conductive coating embedded the anode. The surface was painted with a white acrylic paint.
Temple Street Parking Garage
Award of Excellence: Parking Structures Category
Temple Street Parking Garage
New Haven, Connecticut
Submitted by National Restoration Systems, Inc.
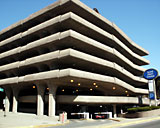
Owner
New Haven Parking Authority
New Haven, Connecticut
Project Engineer/
Designer
Desman Associates
Farmington, Connecticut
Repair Contractor
National Restoration
Systems, Inc.
Rolling Meadows, Illinois
The restoration of the Temple Street parking garage, a very unique concrete structure, was an extremely challenging project. Paul Rudolph designed the Temple Street Garage. Reminiscent of the port of New Haven’s origins; his design combined flowing parabolic curved overhead and vertical concrete surfaces and a unique wooden shiplap texture to convey the stately feel of classic sailing ships.
The New Haven Parking Authority opened this “state-of-the-art” structure in 1962. The ten story split-level multi-use parking facility was originally created as the core for a transformation of the downtown business district. Spanning George Street the structure incorporates 1280 parking spaces and tens of thousands of square feet of retail space. Nothing was spared in Temple Street’s design or construction.
Although concrete deterioration had been periodically addressed, the repairs often did not maintain the look or feel of the original structure. The structural concrete repairs for this renovation were detailed incorporating the unique textures and curves of the original structure. Shoring and forms were designed and custom fabricated to match these surfaces. The deficiencies of past alterations were rectified with these extensive concrete repairs. Hydrodemolition was used to prepare the supported levels of the garage for concrete repairs. An opening was cut within the parking garage’s decks and a new elevator tower was constructed. Today the entire structure meets current standards including those of the Americans with Disabilities Act (ADA).
The restoration was completed over a two-year period at a cost of over eight million dollars. Phases were limited to 200 spaces during the day and 500 at night, ensuring that the parking garage remained in service during the entire project. The completion of this renovation has once again made the Temple Street Garage the flagship of downtown New Haven.
KBP Coil Coaters Structural Fire Repair
Award of Excellence: Special Projects Category
KBP Coil Coaters Structural Fire Repair
Denver, Colorado
Submitted by Restruction Corporation
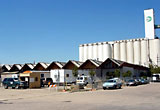
Owner
KBP Coil Coaters
Denver, Colorado
Project Engineer/
Designer
Fay Engineering
Denver, Colorado
Repair Contractor
Restruction Corporation
Sedalia, Colorad
Material Suppliers
Fyfe Co.
San Diego, California
ChemCo Systems, Inc.
Redwood City, California
An extremely hot fire occurred inside a metal coating facility causing serious structural concrete roof structure damage. The building was constructed in the 1950s using a conventionally reinforced concrete folded roof plate slab, designed at 3-1/2-in. thick. The roof span was 85 ft between supports. Significant testing, both destructive and nondestructive was utilized to determine the extent and boundaries of the fire damage. The testing also helped determine the size and location of reinforcing bars. Structural analysis and modeling of the roof plate stresses was completed. The stress distribution models and unique original design eliminated several conceptualized repair schemes.
It was determined that partial depth hydro-demolition was required to insure the highest concrete bond strength and reestablish the concrete to reinforcing steel bond. A wet mix shotcrete was used as the repair material. Epoxy bonded composite materials were installed to assist the repaired roof section in flexure. Trial repairs and subsequent trial testing proved the repair scheme effectiveness. Code analysis of the structure determined that the 1950 code for shear was less stringent than the current code. This was evident as numerous shear cracks were found in the roof plate slab. Epoxy injection was completed to bond the shear cracks. Additional epoxy bonded composites were installed providing additional roof plate slab shear strength.
The Denver Building department required a 4-hour fire rating of the epoxy bonded composites. This stipulation was met. After review of the trial repairs, the building department issued a permit and large scale construction started. Approximately 7140 square ft of concrete repair, 60,000 square ft of epoxy bonded composite and 3150 lineal ft of crack injection was completed.
Hopkins and Clinton Streets Bridge Rehabilitation
Award of Excellence: Transportation Category
Hopkins and Clinton Streets Bridge Rehabilitation
Defiance, Ohio
Submitted by Sika Corporation
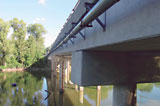
Owner
Defiance County
Defiance, Ohio
Project Engineer/
Designer
Foster Engineering, Inc.
Hamilton, Ohio
Repair Contractor
Structural Preservation Systems, Inc.
Trenton, Michiga
Material Suppliers
Sika Corporation
Lyndhurst, New Jersey
Project Testing
The University of Dayton
Dayton, Ohio
The Hopkins and Clinton Street Bridges in the City of Defiance, Ohio were selected by the Innovative Bridge Research and Construction (IBRC) Program of the Federal Highway Administration (FHWA) for rehabilitation using advanced composite materials and structural health monitoring. After the completion of the repairs, the two bridges will be monitored for a period of at least two years for load-rating, stress and strain patterns, and deflections to determine the long-term effectiveness of the repairs.
Due to the significant deterioration of the prestressed strands in the bridge, coupled with extensive cracking and spalling of the concrete, a carbon fiber system was designed to restore the flexural strength of the beams. However, to optimize the high strength of the carbon fibers and replace the strands, of which approximately 25% were lost in the selected beams, it was decided to use an innovative method of post-tensioning the carbon fibers. This was the first time this post-tensioning system would be utilized in the United States and only the sixth time worldwide.
The main advantages of using a post-tensioned, carbon fiber system for structural strengthening were the high tensile capacity of the plates, the noncorrosive nature of the fibers, the ability to relieve strain in the existing tendons, and the ability to attach the plates to the concrete beams both by mechanical and chemical means to ensure a safe and long-lasting repair.
In addition to strengthening all the affected beams, the bridge bearings were repaired and aligned, the deck drainage was redesigned and replaced, the deck
was waterproofed, and a new wearing course was placed on the bridge. All the deteriorated concrete was removed and replaced with a polymer-modified repair mortar and the exposed mild steel was coated with an anticorrosion coating. These repairs will enable the two bridges to be serviceable for many more years to come, and the cost of repairs was a fraction of what it would have cost the state for removal and replacement.
Renovation of Baltimore's Historic Hippodrome Theater
Award of Merit: Historic Category
Renovation of Baltimore's Historic Hippodrome Theater
Baltimore, Maryland
Submitted by Structural Preservation Systems, Inc.
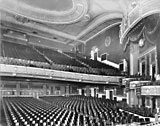
Owner
Maryland Stadium Authority
Baltimore, Maryland
Project Engineer/
Designer
Morabito Consultants
Baltimore, Maryland
Repair Contractor
Structural Preservation
Systems, Inc.
Elkridge, Maryland
Material Suppliers
Hardwire, LLC
Pocomoke City, Maryland
Sika Corporation
Lyndhurst, New Jersey
Built as a vaudeville house around 1914, the Hippodrome is one of the last historic Thomas Lamb theaters in existence. Closed since 1981, the Hippodrome was slated for a renovation that would make it a 2200-seat performing arts complex, transforming it into the city’s prime venue for Broadway shows. Improving a historic structure, however, presents unique challenges. More than needing a “sprucing up”, the theater had to meet the needs of the patrons and the considerably more stringent structural and safety requirements of today.
Investigation of the structure revealed that while the structural steel was in good condition, the huge concrete balcony was in need of extensive repair. Additionally, the structural restoration had to allow for the installation of vent openings at any location without affecting the system’s structural capacity. To do so, a means of upgrading the treads was developed so that they would assume all the design loads, including the dead weight of risers.
The balcony also needed additional reinforcement to the risers to prevent cracking. To accomplish this, an innovative steel reinforced polymer, which was the first commercial use of the product in the U.S., was utilized. This new technology reduced costs, saved valuable time, and provided the advantage of the high-shear strength of a composite system.
This project, completed in only 6 weeks, demonstrates how specialized concrete technology can not only overcome difficult challenges, but can also be key in translating design into reality and, in this case, restoring Baltimore’s prominent landmark to its original beauty.
Restoration of the Ca'd'Zan Mansion
Award of Merit: Historic Category
Restoration of the Ca'd'Zan Mansion
Sarasota, Florida
Submitted by Schnell Contractors, Inc.
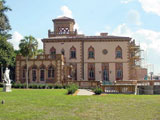
Owner
Florida State University
Tallahassee, Florida
Project Engineer/
Designer
Manausa Lewis & Dodson
Architects
Tallahassee, Florida
Repair Contractor
Schnell Contractors, Inc.
Louisville, Kentucky
Material Supplier
Sika Corporation
Lyndhurst, New Jersey
The Ca’d’Zan Mansion, John and Mabel Ringling’s Venetian Gothic mansion, is one of America’s important historic houses. Renowned architect Dwight James Baum of New York supervised the actual construction.
The concrete foundation wall, which supports the mansion, as well as the exterior 8000 square ft of terrace that overlooks Sarasota Bay, was beginning to show evidence of concrete deterioration. Immediately above this wall was the 1-1/2 story main living room. The support columns between the ornate European doors were finished with stucco on the exterior and encased with onyx marble on the interior side, and cracking could be seen within these concrete support columns on the stucco side. The cracking problem was caused by the oxidation of the existing reinforcing steel within the columns and possibly within the cast concrete arches over the windows. Some of the cracking was also determined to be the result of the weakening of the foundation wall below.
Due to the historical significance of this 1925-1926 mansion, performing these structural repairs was going to require significant preplanning not only to perform the repairs but to maintain the day to day operations of this tourist attraction. The work, structural in nature, also required the need to remove significant historic features which covered the structural elements. These included removal of the European tinted glass doors valued at an estimated $250K each, removal of the 1925 imported onyx marble, and the strategic hand removal of custom terra cotta column capitols and archway pieces.
The repairs had to be done during the occupancy of the structure. Logistical problems such as pedestrian protection and access to the repair all become major decisions that affected the profitability of the project. Combined with adhering to the above details, the delicacy and cost of replicating the historic materials made this a uniquely challenging project.
Restoration of Two Historic Stadiums in Lakeland, Florida
Award of Merit: Historic Category
Restoration of Two Historic Stadiums in Lakeland, Florida
Lakeland, Florida
Submitted by Sika Corporation
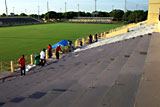
Owner
City of Lakeland
Lakeland, Florida
Project Engineer/
Designer
NHWL
Tallahassee, Florida
Repair Contractor
Above All Caulking & Waterproofing
Tampa, Florida
Material Supplier
Sika Corporation
Lyndhurst, New Jersey
Since 1999, the City of Lakeland, Florida, has been undergoing a major facelift in an effort to attract both businesses and visitors to the downtown area. Projects have included bridges, parking garages, City Hall, building facades and parks. During 2002 and 2003, two adjacent historic stadiums, Henley Field, a baseball stadium built in 1923, and Bryant Stadium, a football stadium built in 1944, underwent major restoration work.
Both stadiums suffered from corrosion of the reinforced concrete, causing cracks and spalls on slabs, columns, and beams. The absence of a waterproof protective coating on the top surface of the grandstands permitted the effects of weathering to erode a significant portion of the cement paste. Loss of the this paste coupled with low reinforcing steel cover and very porous concrete was determined to be the root cause of the corrosion problem.
Spalls were repaired using a combination of “hand-applied” and “form and pour” methods, while dynamic cracks were routed and sealed with polyurethane sealant and static cracks were sealed with epoxy. To protect both new and existing concrete from further deterioration, a low modulus epoxy broadcast overlay was applied to all top-side surfaces of the grandstands. A blending of black, gray and plum colored quartz sand was used to create the impermeable membrane and help hide any bugholes and other surface imperfections in the existing concrete as well as to help conceal dirt and stains generated from events at the stadium.
The cost to rehabilitate both stadiums was approximately $700,000 and took approximately 7 months.
Lanark Distribution Center Project
Award of Merit: Industrial Category
Lanark Distribution Center Project
San Antonio, Texas
Submitted by Surmac, Inc.
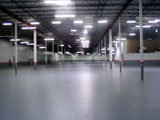
Owner
Cross & Company
San Antonio, Texas
Project Engineer/
Designer
PSI
San Antonio, Texas
Repair Contractor
Surmac, Inc.
San Antonio, Texas
Material Suppliers
Fox Industries, Inc.
Baltimore, Maryland
MAPEI Corporation
Cedar Park, Texas
The Sherwin-Williams Company
Houston, Texas
THR
Bellflower, California
This 157,000 square ft industrial warehouse, located in San Antonio, Texas, offered an amazing opportunity for over 30 years of experience to culminate in an aggressive, cutting-edge, quality, value-oriented process. The warehouse is a concrete tilt-wall, dock high structure with a steel joist and built-up roof system. The warehouse owners were not satisfied by the conventional repair approach that had been offered to them, removing and replacing the slab.
The owners purchased the facility for long-term investment purposes and consulted with a local concrete contractor who assessed that over 40% of the floor would require total removal and replacement. There were expansion and control joint deterioration issues; failed epoxy repairs; a need to remove over 5000 threaded imbedded screws anchored in the floor; dock door thresholds that needed steel structure demolition and rebuilding; and residue accumulated due to prior operations. The concrete damage was a result of a lack of maintenance, overloading, abuse, curling, chemical damage, impact damage, poor mix design and finishing.
The repaired surface offers greater strength, structural integrity, aesthetic value and longevity than that offered by any traditional repair method. Additionally, it is estimated that the owner saved around $100,000, which in today’s economy is no small accomplishment. The elimination of the need to remove a significant amount of concrete prevented much of the traditional waste produced in this type of endeavor.
Riverview Center Parking Garage Repair Project
Award of Merit: Parking Structures Category
Riverview Center Parking Garage Repair Project
Menands, New York
Submitted by Structural Preservation Systems, Inc.
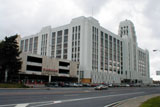
Owner
Loeb Partners Realty
Menands, New York
Project Engineer/
Designer
VStructural LLC
Springfield, Virginia
Repair Contractor
Structural Preservation Systems, Inc.
Hawthorne, New Jerse
Material Suppliers
VStructural LLC
Springfield, Virginia
Watson Bowman Acme Corporation
Amherst, New York
Riverview Center Parking Garage, a facility adjacent to the Riverview Center Office Building in Menands, New York, accommodates approximately 700 vehicles in an area of 200,000 square feet. After decades of experiencing severe freeze-thaw conditions and being exposed to de-icing salts, the 35-year old structure experienced failure at the second supported level.
A full condition assessment was conducted including chloride ion testing, post-tensioning system probes, chain drag/hammer sounding, and petrographic analysis. Upon completion of the comprehensive survey, a multi-step repair program was developed.
Several design considerations were part of the repair program. Most crucial of these were the failed second supported level and the repair to all of the cantilevered expansion joints. Each project challenge was met including an innovative repair strategy for the second supported level. This project also had a number of construction considerations including cost-saving scheduling measures, precautions taken to protect building occupants and quality control initiatives.
The Riverview Center parking garage repair project was performed under a team-oriented, design-build approach involving the engineer, the contractor and the owner. The project is an excellent example of how a successful solution-oriented collaboration between the owner, the engineer and the contractor can optimize time, economics and repair solution options.
Repair of Return Activated Sludge Pumps
Award of Merit: Special Projects Category
Repair of Return Activated Sludge Pumps
Menands, New York
Submitted by Structural Preservation Systems, Inc.
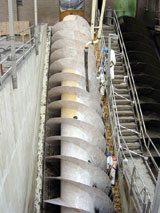
Owner
Passaic Valley Sewerage Authority
Newark, New Jersey
Project Engineer/
Designer
Engineering Department
Passaic Valley Sewerage Authority
Newark, New Jersey
Repair Contractor
Spectraserv
South Kearney, New Jersey
Material Suppliers
Degussa Building Systems
Shakopee, Minnesota
Siegel Brothers Supply Company
Brooklyn, New York
In a waste treatment facility, the owner needed to replace the “Archiamedes” pump screw that moves the sewage from the influent tank below, up a 28-degree angle channel into the processing holding tanks. This facility has the 3 largest types of these pump screws in the world. In conjunction with the pump screw replacement, a full repair of the concrete channel in which the effluent moves upward, was done, as this channel showed severe deterioration of the concrete from abrasive wear and chemical attack.
Because of the tight tolerance needed between the pump blades and the channel walls, forming the channel and subsequently pouring to those exacting tolerances was essentially prohibited. The method employed was to first install the pump screw to an operational status and then use the operating screw to place the repair concrete exactly where it needed to be. Once it had set to the point where the masons could finish, the pump was turned off and the finishers rendered the surface to the point where an epoxy coating could be applied.
This project was unique because of the unconventional nature of the delivery/placement of the material where the synergies between repair and service were utilized to make a successful repair strategy. Continuous operation was essential. The ability to stage, mix and deliver in a continuous operation was helped by having a material that had the working time capable of doing the project.
Promenade Plaza Rehabilitation and Strengthening
Award of Merit: Strengthening Category
Promenade Plaza Rehabilitation and Strengthening
Bethesda, Maryland
Submitted by C.A. Lindman, Inc.
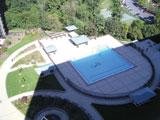
Owner
The Promenade Towers Mutual
Housing Corporation
Bethesda, Maryland
Project Engineers/
Designers
Seal Engineering, Inc.
Alexandria, Virginia
Smislova, Kehnemui & Associates
Rockville, Maryland
Carl Walker, Inc.
Kalamazoo, Michigan
Stephenson & Good
Alexandria, Virginia
Repair Contractor
C.A. Lindman, Inc.
Jessup, Maryland
Material Supplier
Sika Corporation
Annapolis, Maryland
The Promenade Plaza Restoration project in Bethesda, Maryland had been in planning for over 10 years before the actual construction started in late 2002. The plaza is a spacious 115,000 square ft of elevated plaza, bordered on two sides by high-rise buildings, and sits over a three-story garage.
The project consisted of concrete repair, waterproofing, a combination steel/carbon fiber strengthening, post-tension repair, and the installation of landscape and archi-tectural featured finishes. This was all in one project, with three consultants all hired by and working directly for the owner, one contractor, and a material supplier providing another design consultant. Yes, this project had FOUR independent design professionals—each had a separate contract, and none worked under the other.
The final project, completed in 2003, had over 336,000 pounds of structural steel installed, and approximately 33,000 lineal ft of carbon fiber strips installed. Because of the fast track nature of the project, changes to the work were common. The job of explaining these changes to the owner, in a room with the consultants the owner was paying, fell to the rehab consultant, who did an excellent job of handling all of the political “hot potatoes.”
Repair of S.R. 92 Bridge over Noon Day Creek
Award of Merit: Transportation Category
Repair of S.R. 92 Bridge over Noon Day Creek
Cherokee County, Georgia
Submitted by Structural Composites, Inc.
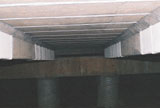
Owner
Georgia Department of Transportation
Atlanta, Georgia
Project Engineer/
Designer
J.B. Trimble & Associates
Atlanta, Georgia
Repair Contractor
Engineered Restoration Company
Lawrenceville, Georgia
Material Suppliers
B.G International LLC
Riverwood, Maryland
Structural Composites, Inc.
Houston, Texas
In the last two decades, many of Georgia’s bridges have been widened to meet increasing capacity demands. Originally, these bridges were often designed for the H15 truck loading, and 15 psf of future wearing surface. If the sufficiency rating is high enough, the H15 section of the bridge is retained and incorporated into the new bridge width. New sections of a widened bridge are designed for the current live loading. In the past, no attempt has been made to upgrade the original H15 sections to meet the higher loads because traditional strengthening methods such as external post-tensioning or externally bonding steel plates to the members were cost-prohibitive. Recognizing the need for a solution, GDOT’s Office of Bridge Maintenance decided to find a cost-effective solution to the “sandwich” problem: utilizing fiber-reinforced polymers (FRP).
Built in 1962, S.R. 92 over Noon Day Creek in Cherokee County, was a 26 ft wide by 160 ft long bridge composed of five 32-ft long reinforced concrete T-beam spans. The original section of the bridge would require a 30% increase in both flexure and shear capacity. The method of FRP shear strengthening used for this project was unique. Drawing from recent research on carbon fiber shear strengthening, special L-shaped brackets were used.
The carbon fiber installation was completed in only 50 days using daytime single-lane closures. A total of 1000 square ft of carbon fiber laminate was installed on the beams and slab, upgrading roughly 3900 square ft of bridge.
Sutro Reservoir
Award of Merit: Water Structures Category
Sutro Reservoir
San Francisco, California
Submitted by Sika Corporation
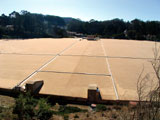
Owner
San Francisco Public
Utilities Commission
San Francisco, California
Project Engineers/
Designers
Mitchell Engineering
San Francisco, California
San Francisco Public Utilities Commission
San Francisco, California
Repair Contractor
Lotus General Contractors
Emeryville, California
Material Supplier
Sika Corporation
Lyndhurst, New Jersey
The Sutro Reservoir is owned and operated by the San Francisco Public Utilities Commission (SFPUC). Completed in 1952, the reservoir contains approximately 32 million gallons of potable drinking water for the City of San Francisco. The lid of the reservoir was showing signs of significant distress including failed expansion joints, cracking of the concrete deck throughout and spalling of the deck and supporting beams.
A comprehensive investigation was conducted by SFPUC to determine the extent of the deterioration and devise a repair and protection system to extend the life service of the structure.
Unique to this project was the use of zodiac boats to inspect the underside of the lid and divers to inspect areas under the waterline.
This awards entry focuses on the work related to repairing and protecting the top side and underside of the 300,000 square ft lid of the reservoir, a critical source of drinking water for the City of San Francisco, California.