Project of the Year: Parking Structures Category
Grant Park South Garage Rehabilitation
Owner
Chicago Park District
Chicago, Illinois
Project Engineer/
Designer
Walker Parking Consultants
Chicago, Illinois
The Grant Park South Garage is an underground parking facility originally constructed in 1963, and located in downtown Chicago, Illinois. The four-level facility includes three underground parking levels. The top or fourth level supports portions of Grant Park, Michigan Avenue, and Jackson Street. The structure includes 536,000 square feet (49,800 square meter) and 1300 parking spaces, with high parking demand that fills the spaces several times per day.
The rehabilitation provided long-term solutions to correct structural deterioration, provide operational enhancements, and modernize other aging systems in the garage. The primary concrete repairs included full-depth slab replacement for the garage and Michigan Avenue concrete slabs. The slab replacements included calcium nitrate corrosion inhibitor and moisture protection systems. Concrete repairs were provided at the lower level garage slab that is also the primary garage foundation mat. Partial depth concrete repairs were used to minimize difficulties in keeping the existing parks and street operations in place during the entire construction project. Hydrodemolition was used to remove the top 3 inches (7.6 cm) of concrete and provide a new concrete environment (microsilica and calcium nitrate) around all foundation slab top bars. Pedestrian stairways also required repair and reconstruction of the concrete stair support structures.
Cost control for the new structural, electrical, architectural, mechanical and preventative maintenance requirements included life cycle cost analysis and service life evaluations. The construction manager and design team developed the phasing to allow the roadway construction and garage construction to alternate – thereby keeping the construction crews to a uniform large size. This approach reduced remobilization costs and kept the construction moving at an accelerated pace.
The rehabilitation provided a cost effective solution and extended the service life by more than 25 years. The improvements enhanced operations and updated the garage for new building codes and laws. The garage will be able to continue operations with minimal operational or maintenance costs and generate revenues for Park District programs.
Award of Excellence
Seven Sisters Generating Station Rehabilitation Longevity - Vector Construction Group
Award of Excellence: Longevity Category
Seven Sisters Generating Station Rehabilitation
Seven Sisters, Manitoba, Canada
Submitted by Vector Construction Group
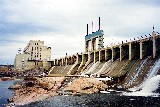
Owner
Manitoba Hydro
Winnipeg, Manitoba, Canada
Project Engineer/
Designer
Manitoba Hydro
Winnipeg, Manitoba, Canada
Repair Contractor
Vector Construction Group
Winnipeg, Manitoba, Canada
In 1979, a major rehabilitation program was undertaken on the Seven Sisters Generating Station to extend the life of the structure for an additional 50 years. The rehabilitation consisted of rebuilding the North non-overflow dam, replacing 13 spillway piers, replacing portions of two sluiceway piers, replacing portions of the sluiceway rollways, and installing insulation and new overlay slab on the spillway rollway.
The rehabilitation was required for several reasons. First, to replace concrete that was extremely low strength as a result of its original mix and placing technique. Secondly, to alleviate concerns about the freeze-thaw damage within the structure and loss of mass from concrete loss due to freeze-thaw damage on the surface. All this was critical due to the original design having a very low safety factor for overturning.
The nature of the rehabilitation required the use of many innovative solutions, in the design, materials and construction techniques. The project’s success was due, in a large part to the synergistic cooperation between the owner and repair contractor in shared ideas and an openness to try new and innovative methods. The result of this innovation and synergy was a project that was completed one year ahead of schedule and over $2,000,000 under budget.
Looking at the spillways and sluiceway today, over 20 years later, they have performed as they were expected and show no signs of deterioration. There appears to be little trouble meeting the expectation of another 30 years of successful performance of the structure.
University of Kentucky Parking Structure #2 Restoration and Expansion Parking Structures — Carl Walker, Inc.
Award of Excellence: Parking Structures Category
University of Kentucky Parking Structure #2 Restoration and Expansion
Lexington, Kentucky
Submitted by Carl Walker, Inc.
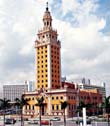
Owner
University of Kentucky Procurement & Construction
Lexington, Kentucky
Project Engineer/
Designer
Carl Walker, Inc.
Kalamazoo, Michigan
General Contractor
Messer Construction Co.
Lexington, Kentucky
Repair Contractor
Schnell Contractors
Louisville, Kentucky
Material Suppliers
3M Corporation
St. Paul, Minnesota
Architect
GBBN Architects
Lexington, Kentucky
This $9,300,000 restoration project located on the main campus of the University of Kentucky (UK) involved in the restoration and expansion of a 5-level 800-space parking structure built in 1969. The structural system consists of cast-in-place post-tensioned concrete beams and one-way slabs. The primary slab reinforcement consists of unbonded button-headed post-tensioning tendons, with little or no supplemental mild reinforcing steel. A bonded button-headed post-tensioning system was used in the beams.
The existing parking structure was in poor condition, with up to 50% of the slab primary post-tensioning tendons broken or severely damaged due to chloride-induced corrosion. The other primary restoration challenge involved restraint issues. The original structure was tied to stiff stair tower elements in each of its four corners, which restrained the natural movement of the slab. This resulted in excessive tensile stresses in both the slabs and the stair tower elements that led to severe cracking on these areas.
A structural steel framing system was implemented to supplement the structural slabs to compensate for the deterioration of the primary slab tendons. This innovative repair approach resulted in lower costs, a more compressed construction schedule and far less disruption to existing operations. A total of 1365 steel beams were installed which included over 5000 epoxy anchorages for the connections. Some selective post-tensioning repairs were also completed.
The restraint problems were addressed by separating the stairs from the main structure by severing slab and beam elements. This involved complex detailing as the main structure slabs and beams were supported by the stair elements. This required redesign and re-anchoring of the post-tensioning tendons.
Structural Repairs to the Catholic Church of St. Joseph Special Projects — Construction Technology Laboratories, Inc.
Award of Excellence: Special Projects Category
Structural Repairs to the Catholic Church of St. Joseph
Menomonie, Wisconsin
Submitted by Construction Technology Laboratories, Inc.

Owner
St. Joseph Parish
Menomonie, Wisconsin
Project Engineer/
Designer
Construction Technology Laboratories, Inc.
Skokie, Illinois
Repair Contractor
Oscar J. Boldt Construction
Stevens Point, Wisconsin
Material Supplier
Conway Universal Studios (Stained Glass Restoration)
Winona, Wisconsin
The Catholic Church of St. Joseph in Menomonie, Wisconsin, was built in 1963. Its most innovative and expressive architectural feature is its saddle-type, hyperbolic paraboloid concrete shell roof. At the southeast corner of the structure, the roof shell projects outward beyond the exterior walls to form a canopy over the main entrance. This canopy is supported by its continuity with the roof shell and by two brick masonry fin walls that project outward from the main walls toward the canopy shell edges. These fin walls extend upward from grade approximately 50 feet to the curved soffit of the canopy shell.
The church’s original designers had only closed-form methods to analyze the shell structure, and their design for the canopy pushed the limitations of the available analysis methods. After 36 years in service, the fin walls had bowed, the masonry was cracked, and the tops of the fin walls had displaced significantly. The fin walls were slipping out from beneath the canopy, and as a result, large sections of masonry were in danger of falling and the roof structure was on the verge of serious damage.
Using techniques unavailable at the time of original construction, engineers developed a finite element model of the church structure to study the condition of the structure and the fin wall/canopy interaction. The model was subjected to gravity loads, creep, and seasonal thermal changes, and then used to identify structural demands on the fin walls. This led to an understanding of the observed behavior and an appropriate repair design, including shoring methods to support the shell during the repairs.
The investigation and repairs not only averted a potentially dangerous failure, but also preserved the building’s architectural character and allowed the church to remain in use through the entire course of reconstruction. Matching brick from the original supplier were used to construct new reinforced masonry fin walls. Original stained glass windows were carefully removed, stored, and reinstalled in the strengthened structure. The investigation and repairs saved this landmark church and helped extend its useful life for many years to come.
Rehabilitation of La Rioja Bridge Transportation — MBT Colombia S.A., Degussa Construction Chemicals
Award of Excellence: Special Projects Category
Rehabilitation of La Rioja Bridge
Puente La Rioja, Colombia
Submitted by MBT Columbia S.A., Degussa Construction Chemicals
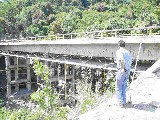
Owner
Gobernacion De Cundinamarca
Bogotá, Colombia
Project Engineer/
Designer
Concesionaria del Desarrollo Vial de la Sabana—DEVISAB
Chia, Cundinamarca, Colombia
Repair Contractor
Consorcio CADSA G y P
Bogotá, Colombia
SESAC LIMITADA
Bogotá, Colombia
Material Supplier
MBT Columbia S.A., Degussa Construction Chemicals
Bogotá, Colombia
This project involves unique rehabilitation of an existing bridge which was kept operational for traffic during its rehabilitation. The only shutdowns involved a 16-hour outage for special jacking of the decks. The approach slabs were sequentially demolished and replaced with a special high-early strength developing concrete.
Unique applications of repair techniques and products involved the structural seismic upgrading with carbon-reinforced composites and strengthening/stiffening of the columns increasing their sections and using special shear connectors. Fluid self-consolidating concrete with fibers was used in the beams and columns to handle traffic-induced vibration during construction.
The beams were jacked up and new neoprene pads were placed. Also, the deck was repaired and strengthened using shear connectors and an overlayment.
Arizona Dam Spillway Repair Project Water Structures — Gervasio & Associates, Inc.
Award of Excellence: Water Structures Category
Arizona Dam Spillway Repair Project
Arizona
Submitted by Submitted by Gervasio & Associates, Inc.
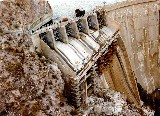
Owner
An Arizona utility company
Arizona
Project Engineer/
Designer
Gervasio & Associates, Inc.
Phoenix, Arizona
Repair Contractor
Truesdell Corporation
Phoenix, Arizona
Material Suppliers
The Euclid Chemical Company
Reno, Nevada
Sika Corporation
Lyndhurst, NJ
This is a concrete repair project consisting of two spillway structures on a hydroelectric dam site in Arizona. Due to security concerns after September 11, 2001, the name of the project, exact location and overall photographs are not allowed to be published.
It is a significant project due to the remote location, extremely difficult access, and the multitude of materials and processes specified and used. The dam site is in a remote area, about an hour-and-a-half drive from civilization. The spillways are situated on shear rocky 200-foot (61-m) high cliffs with the only access from the top of the dam. Significant alkali-silica reactivity (ASR) was occurring, causing excessive cracking, leading to corrosion and spalling.
The engineering investigation survey accessed all parts of the structure using a variety of methods, including a specialty rope access contractor, to determine the extent of deterioration. Specifications were written to allow the contractor the option of many different repair materials and processes for the concrete patching. Lithium was used to treat existing ASR as well as prevent new ASR from occurring at the repair areas.
Construction began in the summer with temperatures on the spillway slab of 130° F (54° C), continuing through the winter with mild freezing temperatures. With a rope access contractor, scaffolding was constructed off the rocky cliffs accessing all parts of the structure. Concrete material, which was chipped off, had to be hauled away and dumped off-site. Dry process shotcrete was used for the patching repairs, as well as epoxy crack injection, polyurethane foam injection, lithium treatments for the ASR, and epoxy flood coats.
Honorable Mention
Sugar Top Resort Facade Restoration High-Rise — Seager Waterproofing, Inc.
Honorable Mention: High-Rise Category
Sugar Top Resort Facade Restoration
Banner Elk, North Carolina
Submitted by Seager Waterproofing, Inc.
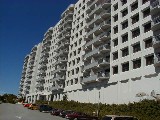
Owner
Sugar Top Resort Condominium Association, Inc.
Banner Elk, North Carolina
Project Engineer/
Designer
Sutton-Kennerly & Associates
Greensboro, North Carolina
Repair Contractor
Seager Waterproofing, Inc.
Greensboro, North Carolina
Material Suppliers
Dow Corning Corporation
Auburn, Michigan
Sika Corporation
Lyndhurst, New Jersey
Guaranteed Supply Company
Greensboro, North Carolina
Sugar Top Resort is an 11-story facility constructed with a concrete main frame, aggregate finished precast panels, projecting residential balconies and individual aluminum window/door units. The original structure was built in 1983 on top of a 5800-foot (1768-meter) high mountain deep in the Appalachians. This facility is three football fields long and totals 320 residential units.
The project is located in Banner Elk, North Carolina, which geographically is a microclimate. The owner has stated that winds have been clocked as high as 180 mph and snow is on the ground every month but July. These conditions are so severe that most doors and windows possessed double units necessary to maintain thermal values.
Twenty years of abuse have resulted in façade issues on this structure. In general, sealants exhibited both cohesion/adhesion type failure; wall coatings were severely blistered; deck coatings were deteriorating from abuse and concrete substrate spalling; handrails were corroding from inadequate protection; and balconies were ponding water from insufficient slope to drain. Because of this, the owner researched and assembled a strong construction team consisting of a competent engineer, product manufacturer and restoration contractor. Plans were generated, bids were received and the final product and contractor were selected on performance-based criteria. The owner recognized that product quality followed by competency in installation were the ingredients to a successful concrete repair project.
Sarasota Harbour West Condominium Repair Low-Rise — The Euclid Chemical Company
Honorable Mention: Low-Rise Category
Sarasota Harbour West Condominium Repair
Sarasota, Florida
Submitted by The Euclid Chemical Company
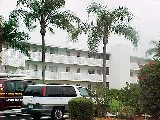
Owner
Sarasota Harbour West Condominium Assoc., Inc.
Sarasota, Florida
Project Engineer/
Designer
Delta Engineering
Sarasota, Florida
Repair Contractor
Diversified Painting and Restoration
Zolfo Springs, Florida
Material Suppliers
The Euclid Chemical Company
Cleveland, Ohio
Construction Chemicals
Sarasota, Florida
Built in 1963, Harbour West is the oldest condominium in the city of Sarasota. The complex consists of four 3-story buildings. Each building has 24 units, for a total of 96 units altogether. The main objective of this repair project was to retain the architecture for the time period that the condominiums were built. Alternatives to restoration, i.e. aluminum rails, were not an option.
The majority of the deterioration within each building was in the stairwell railings and walkway handrails. Each building has a differently designed handrail along the walkways. The varied and unusual design of the railings presented a real challenge to the restoration contractor.
Chloride induced corrosion of the reinforcement resulted in a high number of cracks and concrete spalls throughout the complex. Repairs were necessary in many areas of the condominiums, but the real challenge was in the rails themselves. In many areas, complete railings had to be replaced. The repair contractor was innovative in coming up with ways to replace the concrete while maintaining the unique appearance of each specially designed rail.
The repair system consisted of cementitious/epoxy based coating for the protection of the reinforcement; a one-part microsilica modified, high-slump, flowable repair compound; and a polymer-modified, cementitious repair mortar with a low-slump used for vertical and overhead repairs.
Denver International Airport Level 5 Moisture Protection Parking Structures — Walker Parking Consultants
Honorable Mention: Parking Structures Category
Denver International Airport Level 5 Moisture Protection
Denver, Colorado
Submitted by Walker Parking Consultants
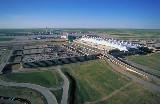
Owner
Denver International Airport
Denver, Colorado
Project Engineer/
Designer
Walker Parking Consultants
Greenwood Village, Colorado
Repair Contractor
John Rohrer Contracting Company, Inc.
Kansas City, Kansas
Material Suppliers
Procoat Systems, Inc.
Denver, Colorado
The Denver International Airport has structured parking for more than 15,000 cars in six separate modules. Built in 1992 and 1993, the structures are precast, prestressed concrete construction with pre-topped, double-tee assemblies with over 5,500,000 square feet (511,000 square meter) of supported surface area. Over 628,000 square feet (58,000 square meter) of microsilica concrete pour strips were placed above column lines and other structural members. Over 150 miles (240 km) of sealant was installed in control joints.
Several years after construction, the structures were experiencing varying degrees of leakage, leaching, ponding of water, corrosion, and other problems at the tee-to-tee joints and pour strips. These were the contributing factors that were causing increasing deterioration of sealants and concrete damage, which was raising considerable concern for long-term durability of the facility. Most parking facilities can easily accommodate planned phasing of investigation, design and repairs. Due to the size and full-time use of the parking structures at DIA, the airport faced potentially significant revenue loss during the restoration process.
A comprehensive design and restoration of the top levels of the facility were completed that incorporated all of the latest technology. It required coordination of the airport management, engineering, and parking operators, along with the consulting engineering firm and the successful restoration general contractor. Through a substantial team effort, the project was investigated, designed, constructed and managed to least impact the facility operators, the parking manager and the general traveling public.
Renovation of the Marshall Field's Parking Facility Parking Structures — Walker Parking Consultants
Honorable Mention: Parking Structures Category
Restoration of the Marshall Field's Parking Facility
St. Paul, Minnesota
Submitted by Buildings Consulting Group, Inc.
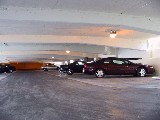
Owner
Marshall Field’s
Minneapolis, Minnesota
Project Engineer/
Designer
Building Consulting
Group, Inc.
Minneapolis, Minnesota
Repair Contractor
Cy-Con, Inc.
St. Paul, Minnesota
Marshall Field’s Department Store in downtown St. Paul, Minnesota was built in 1962, containing 5 stories of retail floors and 7 indoor parking levels that were interconnected. In 1985, the garage was found to have suffered major deterioration due to corrosion of the embedded reinforcing steel, which adversely affected the structural integrity and the appearance of this upscale shopping facility. The Owner was not able to fund the initial $4.5 million construction cost.
The restoration engineer evaluated and established the repair priorities that could allow the Owner to spread the repairs over a 15-to-20 year period for an annual budget of about $250,000, without compromising and jeopardizing the public safety.
In 2002, the repair program was finally completed for a total cost of $4.42 million over 17 years, a cost that is similar to the initial repair budget projection, but only about 45% of the cost for rebuilding a new similar size parking facility for the store. The Owner operated its retail business and parking smoothly without facing any disruption during the entire repair period. The parking garage was completely restored to a safer, more convenient and pleasant pace. The 17-year repair program prevented many patrons, shoppers and visitors from major inconveniences in and around the downtown St. Paul area, where the retail business has been struggling in recent years. The success of this project illustrates the engineering professionals’ ability to assist the Owners, by offering him a workable solution that not only solved his problem, but also prevent the recurrence of the same problem in the future.
Eden Roc Resort and Spa Pool Plaza Restoration Special Projects — C. A. Lindman, Inc.
Honorable Mention: Special Projects Category
Eden Roc Resort and Spa Pool Plaza Restoration
Miami Beach, Florida
Submitted by C.A. Lindman, Inc.

Owner
Black Acre-Capital Hotel Management
Miami Beach, Florida
Project Engineer/
Designer
Willcott Engineers
Margate, Florida
Repair Contractor
C.A. Lindman, Inc.
Pompano Beach, Florida
Material Supplier
Florida Waterproofing Supply
Riviera Beach, Florida
For decades, the Eden Roc Resort and spa has been a famous destination for tourists and sun seekers coming to Miami Beach, Florida. However, deterioration of the hotel’s 70,000 square foot (6500 square meter) concrete pool deck, between the hotel and the beach and over hotel parking convinced the owner that repairs were necessary.
The pool plaza structure consists of both conventionally-reinforced and post-tensioned construction. The goals of the restoration program were twofold: structural and aesthetic. Deterioration to the structural concrete deck and underside beams and columns had to be repaired. Any failed post-tension cables had to be repaired or replaced. The failed waterproofing on the pool deck structural slab had to be removed and replaced. The pool walls themselves required repair of spalled areas. Then, after the structural and waterproofing issues were corrected, the appearance of the pool deck plaza had to be completely modernized.
As important as the work itself was the schedule. During planning and budgeting of the project, the engineer and construction manager had established a 9-month construction schedule. However, the owner did not take bids until early July 2002, and the pool had to be open and available by the end of December 2002. Once the pool and plaza were opened, ancillary work needed to be completed by the end of January 2003. Work in January had to be phased and coordinated with the hotel, so the pool patrons were not displaced.
Strengthening of the "Annex III Building" of the Minas Gerais State Finance Secretary Strengthening — MBT Brasil Ind e Com. Ltda., Degussa Construction Chemicals
Honorable Mention: Strengthening Category
Strengthening of the "Annex III Building" of the Minas Gerais State Finance Secretary
Minas Gerais, Brazil
Submitted by MBT Brasil Ind e Com. Ltda, Degussa Construction Chemicals
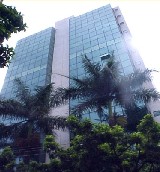
Owner
Secretaria da Fazenda do Estado de Minas Gerais
Minas Gerais, Brazil
Project Engineer/
Designer
Paula Machado Engenharia e Projectos Ltds.
Minas Gerais, Brazil
Repair Contractor
SECOENGE—Servicos de Engeharia Ltda.
Minas Gerais, Brazil
Material Supplier
MBT Brasil Ind e Com. Ltda, Degussa Construction Chemicals
Sao Paulo, Brazil
The main objective of the job was to strengthen the reinforced concrete structures of the Annex II Building, and to correct the original design deficiencies observed on that structure when submitted to transverse wind loads and beyond, allowing the increase of accidental load from 150kg/cm2 to 300kg/cm2.
Due to this wind load situation, the building was closed for almost 15 years. At that time, there was a lack of technologies available to solve the problem. Recent changes of local laws on soil occupation, indicated only one solution—demolition.
When the engineering companies heard about this predicament, they decided to present the owners the CFRP technology, not well known in Brazil, as an ideal solution to upgrade the building structurally.
The solution adopted, applicable on this 13 floor building, was to apply 7650 square feet (710 square meters) of carbon fiber-reinforced polymer (CFRP) System on the 13 floors of the building. Other techniques involved jacking of beams to produce reverse camber before CFRP strengthening.
Repair of Structure Damaged by Overloads at C.C. Commercial Plaza Mayor Strengthening — B.R.S. Ingenieros, C.A.
Honorable Mention: Water Structures Category
Repair Structure Damaged by Overloads at C.C. Commercial Plaza Mayor
Chuao Caracas, Venezuela
Submitted by B.R.S. Ingenieros, C.A.
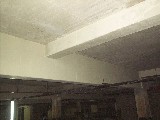
Owner
Consorcio Immobiliaro Plaza
Chuao Caracas, Venezuela
Project Engineer/
Designer
B.R.S. Ingenieros, C.A.
Caracas, Venezuela
Repair Contractor
B.R.S. Ingenieros, C.A.
Caracas, Venezuela
Material Supplier
MBT de Venezuela, C.A.
Caracas, Venezuela
In December 1999, Venezuela was affected by catastrophic floods due to extensive rainfalls that caused great destruction in numerous properties and the lose of many human lives. This project concerns the assessment, design and execution of repair work on a reinforced concrete building that suffered the effects of the overflow of a nearby river that flooded the two lower levels, depositing a large amount of mud and sand; the thickness of the sediment averaged 6.5 feet (2 meters), once water had drained out.
The part of the building that was affected comprises an area of 75,000 square feet (7000 square meters). The structural system was composed of 1 x 2.8 ft (30 x 85 cm) load beams and 1 x 1.3 ft (30 x 40 cm) auxiliary beams in an orthogonal layout. The slabs were 6 in. (15 cm) thick, reinforced in two directions. All columns had a cross section of 1.3 x 1.3 ft (40 x 40 cm). The overload caused the collapse of one sector of the building and general damages extended into the rest of the structure. The damages were mainly shear cracks in beams. The slabs, columns and foundations presented a satisfactory behavior.
A careful evaluation was performed in order to provide a diagnosis and to design the required works for the restoration of the structure based upon the intensity and extension of damages. It was decided to carry out a controlled demolition and reconstruction of the structure in collapsed areas and in parts with severe damages (severe cracks and plastic deformations not recovered in beams). In areas with moderate damages (cracked but without evidence of plastic deformations), the structural properties were restored by the injection of cracks and the application of a composite system based on carbon fiber-reinforced polymers (CRFP).
Interstate Route 480 Bridge Repair Transportation — Vector Corrosion Technologies
Honorable Mention: Transportation Category
Interstate Route 480 Bridge Repair
Omaha, Nebraska
Submitted by Vector Corrosion Technologies
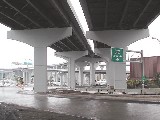
Owner
Nebraska Department of Roads
Omaha, Nebraska
Repair Contractor
Vector Corrosion Technologies
Winnipeg, Manitoba, Canada
In the summer of 2002, the Owner undertook the 3rd phase of a large rehabilitation project on a 1.5 mile elevated section of Interstate Route 480 in downtown Omaha. Constructed in the early 1970s, the viaduct had experienced significant chloride induced corrosion and deterioration to the concrete deck and substructure. The overall project included the rehabilitation of sixty-six hammer-head piers, application of a chloride resistive sealer, and complete deck replacement.
With the replacement of the deck, the long-term performance of the repaired substructure was a concern. In order to extend the service life of the concrete repairs and extend the life of the substructure, Owner elected to perform electrochemical chloride extraction, install embedded galvanic anodes in the patch repairs and apply a chloride resistive sealer to the substructure.
Twenty-three of the hammer-head piers were treated with electrochemical chloride extraction, a technique that removes chloride ions from concrete and restores the rebar to a passive condition. Fifty-five of the piers had embedded galvanic anodes installed within the patch repairs, to extend the life of the patch repairs. Finally a chloride resistive sealer was applied to all sixty-six piers to prevent future chloride contamination.
The application of advanced rehabilitation technologies including chloride extraction and embedded galvanic anodes played a vital role in restoring this structure, and assuring that the substructure will serve as well as the new deck. These technologies allowed the Owner to tailor the level of protection to suit the varying needs of the structure, addressing future corrosion concerns as well as current problems.
JTA Skyway Double Tee Beams Restoration Transportation — Sika Corporation
Honorable Mention: Transportation Category
JTA Skyway Double Tee Beams Restoration
Jacksonville, Florida
Submitted by Sika Corporation
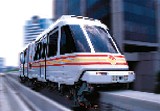
Owner
Jacksonville Transportation Authority
Jacksonville, Florida
Project Engineer/
Designer
Parametrix Engineering, Inc.
Tacoma, Washington
Repair Contractor
Structural Preservation Systems, Inc.
Tucker, Georgia
Material Supplier
Sika Corporation
Jacksonville Beach, Florida
The Jacksonville Transit Authority (JTA) Skyway is a 2.5 mile elevated automated people mover system that serves downtown Jacksonville, Florida. It is a major part of the master plan for the downtown area, while alleviating a growing parking and congestion problem in the city. The Skyway was built in phases for a total cost of $184 million. Starter Line service began in 1988 with full system implementation completed in November 2000. The system is completely computerized ensuring that the trains operate smoothly on the elevated tracks.
A little more than a year after the last segment of the Skyway was completed, engineers noticed the presence of numerous hairline cracks in the precast concrete guideway beams that support the monorail track. After further analysis, it was determined that excessive debonding of the prestressing tendons caused the cracks. A cause for concern, it posed no immediate danger to the Skyway. Nevertheless, some temporary supports were installed while a determination was made on how to repair these cracks. At no time was service interrupted on the system. A total of 63 beams ends were affected, which makes up approximately thirteen percent of the 500 concrete beams in the Skyway.
After careful consideration, the engineers considered five different repair scenarios. A ranking system was established, rating the possible repair techniques by criteria such as durability, maintenance, aesthetics and cost. Ultimately, the solution chosen was a carbon fiber reinforced polymer, externally bonded onto the ends of the deficient beams, that would compensate the strength lost due to the debonded strands.
Rehabilitation of Charlotteburg Reservoir Dam Water Structures — Sika Corporation
Honorable Mention: Water Structures Category
Rehabilitation of Charlotteburg Reservoir Dam
West Milford, New Jersey
Submitted by Sika Corporation
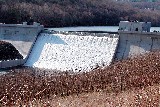
Owner
City of Newark
Newark, New Jersey
Project Engineer/
Designer
Civil Dynamics
Stockholm, Sweden
Repair Contractor
Hutton Construction
Cedar Grove, New Jersey
Material Supplier
Associated Technologies, Inc.
Camden, New Jersey
Sika Corporation
Wayne, New Jersey
The Charlotteburg Reservoir Dam is a vital resource to the State of New Jersey, providing most of the drinking water to the cities of Newark, Bellville, Cedar Grove, and Livingston. It was built in 1960 when the Pequannock River was dammed upstream to create the reservoir. Other than minor repairs, no rehabilitation had taken place on the dam or reservoir during the past 43 years that it has been in service. The reservoir has a total capacity of 3 billion gal. and approximately 45 to 60 million gal. flow out of the structure each day for the cities that it serves. It is located approximately 35 mi northwest of Newark and about the same distance from New York City.
The Charlotteburg Dam was plagued with a number of serious problems, including very large voids (over 2 ft in depth) in the face of the spillway, deteriorated concrete on the spillway and wing walls, leakage and water infiltration into the maintenance buildings and tunnels beneath the dam, and large cracks and leaking joints throughout the structure.
The contractor was challenged with repairing all this deteriorated concrete while still maintaining full service of the reservoir. In addition, the owner and contractor were under additional scrutiny as a result of the terrorist attacks on September 11, 2003. Dams and reservoirs, especially in the New York metropolitan area, were under heightened alert by the Department of Homeland Security due to the concern of contamination from chemical or biological agents. This made the project even more challenging than under normal circumstances.