Project of the Year: Industrial Category
Delayed Coking Unit Turnaround
Southwestern United States
Submitted by Structural Preservation Systems, Inc.
Owner
requests confidentiality
Project Engineer/
Designer
STS Consultants, Ltd.
Green Bay, Wisconsin
Repair Contractor
Structural Preservation Systems, Inc.
Gilberts, Illinois
Material Suppliers/
Manufacturers
Eagle Precast, Inc.
Tulsa, Oklahoma
LaFarge Aluminates
Chesapeake, Virginia
A short duration plant outage or turnaround (T/A) can stretch the limits of a contractor’s ability to physically perform repairs within a limited time frame. Add to the mix a generally hostile environment involving multiple trades sharing essentially the same workspace and conditions can form that may adversely affect the long-term durability of an implemented repair program. Civil infrastructure, when included as part of the T/A “package,” must incorporate innovative approaches and technologies to address time and environmental concerns so the civil works don’t end up affecting the T/A’ s Critical Path Schedule.
Recently, three major, high priority civil infrastructure projects were scheduled concurrently for a Delayed Coking Unit Turnaround (T/A) at a major southwestern U.S. Refinery. Successful implementation of sophisticated construction concepts/processes can only occur when facility owners, engineers, and contractors agree, commit, and execute the vision laid out during original concept, design, review, and construction execution phases of a project. Using advanced engineering, preplanning techniques, and employing sophisticated construction processes, the project was completed on-time and under-budget. The overall approach incorporated innovative project construction phasing, precast, cast-in-place, and post-tensioned concrete element construction technology as well as incorporating extremely durable materials of construction developing a process coined the “T/A Civil Approach” (TCA).
Award of Excellence
One and Four Longfellow Towers Project
Award of Excellence: High-Rise Category
One and Four Longfellow Towers Project
Boston, Massachusetts
Submitted by Sika Corporation
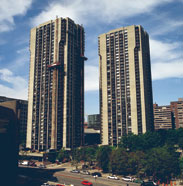
Owner
Equity Residential Properties
Boston, Massachusetts
Assessment Engineer
Simpson Gumpertz and
Heger, Inc.
Waltham, Massachusetts
Repair Contractor
P.J. Spillane Company, Inc.
Everett, Massachusetts
Material Supplier/
Manufacturer
Sika Corporation
Lyndhurst, Maryland
Corrosion Consultant/
Monitoring
Structural HealthCare Associates/C-Probe
Systems, Ltd.
Chelford, Cheshire, England
The prestigious Longfellow complex is located in the heart of downtown Boston on the Charles River. This project focused on two 38-story apartment buildings, constructed between 1970 and 1972. Inspections conducted in 1997 identified numerous areas of spalls due to corrosion of the steel reinforcement. More recently, sealant joints at the sliding glass doors, ac units, and windows were failing and allowing water to leak into the apartments.
In 2001, inspecting engineers carried out a comprehensive investigation to determine the extent of damage and the root cause. Among other things, they determined spalling had increased by 25% since 1996. Exposed column faces, balcony edges, and floor slab edges had the least cover and most spalls. There was chloride contamination, carbonation, and low cover throughout. Wherever the cover was less than 2 in. there was high levels of active corrosion. The goal of the owner and the engineer was to repair the spalled concrete and leaking joints and to provide long-term protection to the building.
A repair program was designed to repair the spalls and leaking joints and protect the building by mitigating active corrosion. A preview was completed to confirm the design met the objectives.
The contractor completed the installation using an organized work plan that was sensitive to the owners scheduling requirements, provided a comprehensive checklist for installation and involved an inspection engineer to confirm compliance with the design documents. Finally, areas of the building were monitored to confirm effectiveness of the repair and protection program. All of this resulted in a repair program that will no doubt provide long-term durability for this owner.
Alcatraz Cellhouse
Award of Excellence: Historic Category
Alcatraz Cellhouse
San Francisco, California
Submitted by Sika Corporation
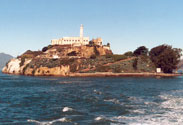
Owner
National Park Service
San Francisco, California
Project Engineer/
Designer
Wiss, Janney, Elstner Associates, Inc.
Emeryville, California
Repair Contractor
Watertight Restoration, Inc.
San Francisco, California
Material Supplier/
Manufacturer
Sika Corporation
Lyndhurst, Maryland
General Contractor
Miller/Watts Construction, Inc.
Richmond, California
Construction Manager
Parsons Brinckerhoff
San Francisco, California
Alcatraz is one of the most famed tourist sites in the United States and welcomes nearly 1.4 million visitors annually. “The Rock” was made famous as a prison that was virtually inescapable because of its remote location in the middle of San Francisco Bay, and its notorious occupants, including Al Capone, “Machine Gun” Kelly, and others.
Alcatraz Cellhouse, the most visited and prominent building on Alcatraz Island, was also the largest reinforced concrete building in the world at the time of its completion in 1912. It was reinforced with square and twisted reinforcing steel, a style that was sometimes used in the early 20th century concrete buildings.
Ironically, what made Alcatraz so famous and difficult for prisoners to escape from was also the cause of its demise. The cold salt waters of San Francisco Bay and the windy conditions of the area caused airborne chlorides to deposit themselves onto the concrete structures, and after decades of exposure and neglect, ultimately penetrate through the concrete to the steel reinforcement. In addition, atmospheric carbon dioxide also caused the concrete to become carbonated over the years, lowering its pH, and causing corrosion of the reinforcing steel. The degradation of the structures on Alcatraz Island, along with the high operating costs of the prison, caused Alcatraz to shut down as a penal institution in 1963.
Alcatraz was occupied by various groups over the next decade with little attention made to maintenance or upkeep. The structures continued to degrade, and chloride induced corrosion caused the reinforcing steel to expand, cracking and spalling the concrete. In 1972, Alcatraz Island was turned over to the Golden Gate National Recreation Area. However, due to limited funds from Congress to the National Parks Service, another 30 years passed before any significant rehabilitation program took place on Alcatraz. When money finally became available, a major concrete repair and seismic strengthening program was initiated.
This was an extremely challenging project for the contractor due to the remote location of the island and the fact that the facility remained open to tourists during construction. In addition, being a landmark building, the appearance of the Alcatraz Cellhouse could not significantly change, including details such as graffiti that were required to remain intact and pipes that could not be relocated.
Rehabilitation of Two Hyperbolic Cooling Towers
Award of Excellence: Longevity Category
Rehabilitation of Two Hyperbolic Cooling Towers
Washingtonville, Pennsylvania
Submitted by CTLGroup
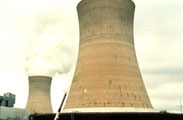
Owner
PPL Corporation
Allentown, Pennsylvania
Project Engineer/
Designer
CTLGroup
Skokie, Illinois
Kline Engineering, PC
Port Washington, New York
Repair Contractor
Pullman Power
Kansas City, Missouri
Material Supplier/
Manufacturer
Sika Corporation
Lyndhurst, New Jersey
Two hyperbolic concrete cooling towers serving a steam electric generating station were put into service in 1972 and 1973. By 1985, they exhibited significant deterioration, corrosion of embedded steel, and water leakage through the shells. These massive towers, which topped out at 370 ft above grade and were as large as 248 ft in diameter, were essential to the plant’s operation. They would need major repairs, which could be carried out only during scheduled outages to avoid disruptions in the area’s power supply.
Scheduling repairs was only one of the project’s challenges. Providing access to the interior and exterior of the towers to allow thorough inspection and repair was difficult. Careful structural analysis was required to maintain the towers’ structural integrity while repairs were under way. Repair materials had to be evaluated and selected for their ability to withstand the unusual conditions within the towers.
To meet these challenges, the power company assembled a multidisciplinary team made up of both staff and consulting engineers. The team included civil engineers, concrete material and construction consultants, structural engineers, and specialists in testing and evaluation.
Using visual inspection, hammer sounding throughout both towers, and laboratory testing of core samples, investigators identified the types and extent of concrete deterioration. In addition to the spalling, corrosion, and leakage already noted, they found cracks in the support columns and ring beams at the bases of the towers.
Repair crews removed the deteriorated concrete from the tower shells with pneumatic chipping hammers and filled the created voids with dry-mix shotcrete. They sealed cooling tower interior surfaces with a water- and vaporproof epoxy coating. They cleaned out cracks in the supporting columns and ring beam and sealed them with epoxy.
Meticulous quality control testing and inspection during repairs helped ensure the project’s success. The work accomplished between 1988 and 1990 has demonstrated its durability and significantly extended the towers’ service life.
Alexandria House Condominium Garage and Plaza Rehabilitation
Award of Excellence: Parking Structures Category
Alexandria House Condominium Garage and Plaza Rehabilitation
Alexandria, Virginia
Submitted by Smislova, Kehnemui & Associates, PA
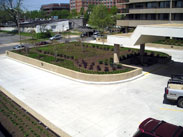
Owner
Alexandria House Council of Co-Owners
Alexandria, Virginia
Project Engineer/
Designer
Smislova, Kehnemui & Associates, PA
Rockville, Maryland
Repair Contractor
Eastern Waterproofing & Restoration Company, Inc.
Jessup, Maryland
Material Supplier/
Manufacturers
ABM Corporation
New York, New York
Lang Tendons, Inc.
Toughkenamon, Pennsylvania
The Alexandria House Condominium Garage and Plaza rehabilitation was a $4.4 million dollar project spanning over 28 months that involved the performance of major structural and waterproofing repairs to the three-level cast-in-place concrete post-tensioned structure. The combination of almost 30 years of inadequate maintenance, poor design details, and poor construction details resulted in severe cracking and deflection of the elevated decks of the parking and plaza areas of the condominium.
Visible signs of distress lead the condominium to conduct an extensive condition survey in late 2000 that included physically exposing and examining a portion of each segment of post-tensioning cable in the elevated decks. Exploratory work revealed areas where over 50% of the cables along a column strip were failed due to corrosion-related deterioration and structure analysis work indicated there were some design deficiencies in the structure. The survey lead to the installation of some permanent emergency shoring in some areas of the garage and the condominium quickly planned a thorough repair program for the facility.
Highlights of the project included the removal and replacement of approximately 34,000 linear ft of post-tensioning cables, the installation of almost 8000 linear ft of carbon fiber reinforced polymer (CFRP) strips for flexural strengthening and slab crack control. The project also included the removal and re-construction of a 15,500 square ft plaza deck area that was severely deteriorated and needed to be upgraded for fire truck loading.
The post-tensioning cable replacement work was made extremely difficult due poor sheathing conditions and out-of-plane paths for the existing cable system. The plaza level deck partial reconstruction was challenging as it involved tying a newly constructed post-tensioned slab into an existing structure while maintaining occupancy of the adjacent plaza areas and the garage parking below.
Soldier Field Stadium Renovation
Award of Excellence: Special Projects Category
Soldier Field Stadium Renovation
Chicago, Illinois
Submitted by National Restoration Systems, Inc.
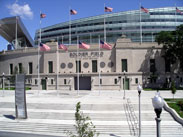
Owner
Chicago Park District
Chicago, Illinois
Project Engineer/
Designer
Thornton-Tomasetti Engineers
Chicago, Illinois
Repair Contractor
National Restoration
Systems, Inc.
Rolling Meadows, Illinois
Construction Manager
Tuner/Barton Marlow/Kenny Joint Venture
Chicago, Illinois
The renovation of Soldier Field Stadium was a massive undertaking. The design retained the historic façade, concrete walkways, and colonnades while grafting a modern stadium facility within its core.
Demolition began the night of a Chicago Bears play-off game on January 19, 2002. A Monday night grand opening game between the Bears and their traditional nemesis the Green Bay Packers was scheduled for September 29, 2003. Liquidated damages of $4.5 million per game would be assessed to any contractor who was responsible for failing to reopen the stadium on time.
The concrete restoration of Soldier Field’s remaining cast-in-place concrete structure was scheduled to begin in March 2002 immediately following the demolition contractor as the original seating bowl was removed. The bowl demolition exposed concrete surfaces that had been hidden for 78 years.
The City Building Commission of Chicago refused to issue a “Repair Permit” without an updated condition survey. All concrete surfaces within the stadium structure had to be sounded, and deteriorated areas were marked with paint, measured, identified by number, and entered on the plans. The permit was issued after a two month delay.
The concrete restoration contractor was faced with a 300% quantity increase, an expanded scope, and a two-month delay with the same completion date. Additional crews and equipment were mobilized. Many critical zones and locations throughout the structure had to be repaired on second shifts and weekends due to worker congestion and safety concerns. Double shifts, seven days a week, were scheduled as necessary to complete the concrete repairs. Over 60,000 square ft of concrete repairs were completed on time under extremely difficult conditions. Quality and safety were always maintained. The crew completed the project on time with a perfect safety record.
Soldier Field Stadium reopened on time.
Old Main Post Office Plenum Ceiling Repair
Award of Excellence: Transportation Category
Old Main Post Office Plenum Ceiling Repair
Chicago, Illinois
Submitted by Degussa Building Systems
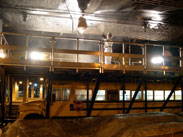
Owner
United States Postal Service
Chicago, Illinois
Project Engineer/
Designer
Parsons Brinckerhoff
Chicago, Illinois
Repair Contractor
Allied Waterproofing, Inc.
Lyon, Illinois
Material Supplier/
Manufacturer
Degussa Building Systems
Shakopee, Minnesota
The Old Main Post Office was completed in 1932. With hundreds of train movements and thousands of passengers using the rail system daily, the Amtrak Station under the Old Main Post Office is a vital link between home and work for many Chicagoans. This 73-year old structure has survived the age of steam and coal fired trains and remains in relatively good conditions despite years of exposure to diesel locomotive exhaust. The ingress of carbon dioxide has reduced the pH of the parent concrete leading to severe corrosion of the structural reinforcing steel. This condition posed a serious risk to both passengers and trains alike.
The main challenge facing the engineer was determining the most effective methods of removing and replacing the damaged concrete. Several means and methods were explored over a two year period leading up to the development of the project specification. Ultimately, the engineer selected low velocity spray applied mortar for the replacement.
The contractors developed a plan to complete the work in a specified time, without shutting down the train station or creating disruption to commuters. All of the smaller equipment and manpower for each night’s work was loaded onto a converted school bus with folding platforms, and pulled to the work area on railroad tracks. The materials, mix water, and spray equipment were placed on a flatbed rail car and towed in behind the school bus. After the completion of each shift of work, the converted school bus drove out of the station and back to a staging area roughly one mile away.
The Old Main Post Office Plenum Ceiling Repair project was a complicated endeavor with many obstacles. By fostering a successful “partnership” between engineer, general contractor, subcontractors, and material supplier, the project was successfully completed on time and on budget.
John Day Dam Navigation Lock Repair
Award of Excellence: Water Structures Category
John Day Dam Navigation Lock Repair
Rufus, Oregon
Submitted by Pioneer Waterproofing Company, Inc.
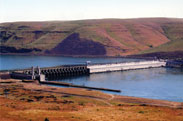
Owner
Army Corp of Engineers
Portland, Oregon
Project Engineer/
Designer
Army Corp of Engineers
Portland, Oregon
Repair Contractor
Pioneer Waterproofing Company, Inc.
Portland, Oregon
Material Supplier/
Manufacturers
ChemCo Systems, Inc.
Redwood City, California
DeNeef Construction Chemicals (US), Inc.
Houston, Texas
The John Day Dam was the last major dam building project competed on the lower Columbia River. Construction began in 1958 and was completed in 1971. The Navigation Lock allows commerce to pass up and downstream and is an important part of the northwest’s economy moving millions of tons of northwest’s agricultural and forest products to be shipped through out the world.
In 2003, over 2500 cracks were discovered in two of the sections of the Lock (called Monoliths), some as large as 2 in. in width which ran the full height of the lock, threatening the structural integrity of the Lock itself. The possibility existed that portions of the Lock could fail collapsing into the Lock, which could close all commercial river traffic on the Columbia River for up to one year. Had this had happened the economic impact on the northwest’s economy would have been in the billions of dollars.
The scope of work on the project involved epoxy injection of up to 2500 lineal ft of concrete cracks ranging in width from 1/8 to 2 in. and varying in depth from 4 to over 15 ft. Most of the cracks to be injected were up to 150 ft in height.
The Lock was required to be shut down during the entire epoxy injection portion of the project. Due to the economic impact of the shut down, the work was required to be completed in no more than 28 calendar days.
Point Brittany 6 Condominium Restoration
Award of Merit: High-Rise Category
Point Brittany 6 Condominium Restoration
St. Petersburg, Florida
Submitted by CPT of Florida, Inc.
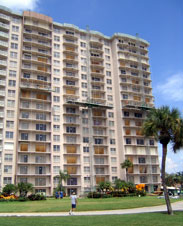
Owner
Point Brittany 6 Condominium
St. Petersburg, Florida
Project Engineer/
Designer
Karins Engineering
Group, Inc.
St. Petersburg, Florida
Repair Contractor
Structural Preservation Systems, Inc.
Sarasota, Florida
Material Suppliers/
Manufacturers
CPT of Florida, Inc.
Cocoa Beach, Florida
Matcor, Inc.
Doylestown, Pennsylvania
Point Brittany 6 is a classic example of an aging 30-year old Florida condominium that needed major repairs on its 30,000 square feet of balconies. The guardrails on the balconies were constructed of pre-cast reinforced concrete elements and were a significant architectural element of the building. In 1996, a major restoration project included the addition of welded steel stanchions to improve the support of the pre-cast guardrail system. During that repair, a penetrating waterproofing agent was also applied to the balcony slabs. In 2003, the Board hired an engineer to survey the ongoing balcony and guardrail damage. They determined that the existing pre-cast concrete guardrails could not be repaired and should be replaced.
Because this was the second major restoration project in just a few years, the Board investigated using impressed current cathodic protection as a more permanent means of protecting the reinforced concrete balcony slabs. The concrete restoration and balcony waterproofing portion of the work would be around $800,000 if it was a traditional chip and patch repair and waterproofing project. The incremental cost of the impressed current cathodic protection system was approximately $110,000. Using the current cost of repair as a lower bound for the likely cost of repairs in the next likely repair cycle, the Board determined that the incremental cost of the impressed current cathodic system would be a good investment.
The entire project included repair of deteriorated pre-cast window sills, deteriorated stucco, reinforced concrete repair, installation of the cathodic protection system, waterproofing of the building envelope and replacement of all perimeter handrails with a welded aluminum system. To date, this is one of the largest high rise residential buildings on the west coast of Florida to install an impressed current cathodic protection system (ICCP).
Cardinal Gibbons Fine Arts Building Restoration
Award of Merit: Historic Category
Cardinal Gibbons Fine Arts Building Restoration
Baltimore, Maryland
Submitted by Structural Preservation Systems, Inc.
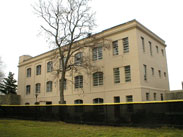
Owner
The Cardinal Gibbons School
Baltimore, Maryland
Project Engineer/
Designer
Archdiocese of Baltimore
Baltimore, Maryland
Repair Contractor
Structural Preservation Systems, Inc.
Elkridge, Maryland
Material Suppliers/
Manufacturers
TAMMS Industries, Inc.
Kirkland, Illinois
U.S. Concrete Products
Timonium, Maryland
Originally constructed in the late 1800s, the Fine Arts Building on the Cardinal Gibbons School campus is an important historic landmark for the City of Baltimore, yet the structure was in disrepair. Formerly known as St. Mary’s Industrial School, the facility served as an institution for delinquents and orphan boys, including baseball great Babe Ruth.
With perimeter dimensions of approximately 120 x 60 ft, the three-story concrete reinforced structure has an ornamental cornice comprised of concrete. Initial inspections revealed that the cornice had severe deterioration primarily due to the existing gutter and downspout system that was non-functional. Additional deterioration was found on the concrete façade and parapet where the existing coating was no longer effective. The primary causes of deterioration were due to initial construction defects along with initial construction shrinkage cracking, failure of the existing coating and drainage systems, acidic gases predominant in metro-politan areas and the natural permeability of concrete.
The most difficult repair was the cornice. New reinforcing steel was added to the cornices due to the lack of sufficient existing steel. Plaster of Paris was used to make a mold of an existing sound section of the cornice and then fiberglass forms were developed. Several mockups were made prior to achieving the desired result, which was versatile enough to match all inconsistent field conditions of the cornice. Once the formwork was complete, the cornices were poured. Upon completion, the final project cost was less than the estimate.
Today, because of the innovative concrete repair strategies and the effort to not only salvage but also bring new life to the structure, the building stands poised to meet the demands of tomorrow’s students.
Johns Hopkins Hospital Broadway Buildings Exterior Restoration
Award of Merit: Historic Category
Johns Hopkins Hospital Broadway Buildings Exterior Restoration
St. Petersburg, Florida
Submitted by CPT of Florida, Inc.
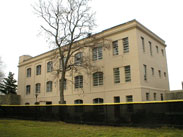
Owner
Johns Hopkins Hospital
Baltimore, Maryland
Project Engineer/
Designer
Kann & Associates
Baltimore, Maryland
Repair Contractor
Watts Restoration, Inc.
Croydon, Pennsylvania
Material Suppliers/
Manufacturers
Cathedral Stone
Products, Inc.
Hanover, Maryland
Tom Brown, Inc.
Phoenixville, Pennsylvania
Work on this project included demolition and construction for exterior restoration of the Marburg, Billings and Wilmer Buildings, which comprise the historic front façade of the Johns Hopkins Hospital. The John Shaw Billings Building is the signature of the campus and its dome is featured in the hospital’s logo and graphics.
The buildings are comprised of limestone and brick. Water infiltration and deterioration of the limestone and masonry prompted the repair project.
Site preparation included full scaffolding and shoring of the façade. It was constructed from grade level to the upper dome roof on all elevations.
A major challenge of the project was that the dome was composed of “Lime of Teil” block on the interior and certain portions of this were called to be removed and replaced. Original product to use for replacement was impossible to find due to age of the building which dates back to May 5, 1889.To rectify the problem, the contractor made molds and cast new “Lime of Teil” blocks for the dome from the restoration mortar.
Special features of this project are the reconstruction of the exterior dome finials. Also, the reconstruction of the ornamental limestone was extremely difficult and time consuming. The project included the limestone patches, as well as façade cleaning and finial panel exterior waterproofing.
Point Brittany 6 Condominium Restoration
Award of Merit: High-Rise Category
Point Brittany 6 Condominium Restoration
St. Petersburg, Florida
Submitted by CPT of Florida, Inc.
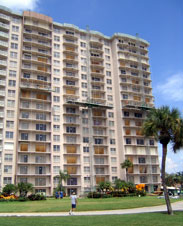
Owner
Point Brittany 6 Condominium
St. Petersburg, Florida
Project Engineer/
Designer
Karins Engineering
Group, Inc.
St. Petersburg, Florida
Repair Contractor
Structural Preservation Systems, Inc.
Sarasota, Florida
Material Suppliers/
Manufacturers
CPT of Florida, Inc.
Cocoa Beach, Florida
Matcor, Inc.
Doylestown, Pennsylvania
Point Brittany 6 is a classic example of an aging 30-year old Florida condominium that needed major repairs on its 30,000 square feet of balconies. The guardrails on the balconies were constructed of pre-cast reinforced concrete elements and were a significant architectural element of the building. In 1996, a major restoration project included the addition of welded steel stanchions to improve the support of the pre-cast guardrail system. During that repair, a penetrating waterproofing agent was also applied to the balcony slabs. In 2003, the Board hired an engineer to survey the ongoing balcony and guardrail damage. They determined that the existing pre-cast concrete guardrails could not be repaired and should be replaced.
Because this was the second major restoration project in just a few years, the Board investigated using impressed current cathodic protection as a more permanent means of protecting the reinforced concrete balcony slabs. The concrete restoration and balcony waterproofing portion of the work would be around $800,000 if it was a traditional chip and patch repair and waterproofing project. The incremental cost of the impressed current cathodic protection system was approximately $110,000. Using the current cost of repair as a lower bound for the likely cost of repairs in the next likely repair cycle, the Board determined that the incremental cost of the impressed current cathodic system would be a good investment.
The entire project included repair of deteriorated pre-cast window sills, deteriorated stucco, reinforced concrete repair, installation of the cathodic protection system, waterproofing of the building envelope and replacement of all perimeter handrails with a welded aluminum system. To date, this is one of the largest high rise residential buildings on the west coast of Florida to install an impressed current cathodic protection system (ICCP).
Johns Hopkins Hospital Broadway Buildings Exterior Restoration
Award of Merit: Historic Category
Johns Hopkins Hospital Broadway Buildings Exterior Restoration
Baltimore, Maryland
Submitted by Watts Restoration, Inc.
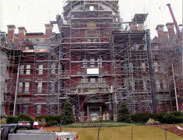
Owner
Johns Hopkins Hospital
Baltimore, Maryland
Project Engineer/
Designer
Kann & Associates
Baltimore, Maryland
Repair Contractor
Watts Restoration, Inc.
Croydon, Pennsylvania
Material Suppliers/
Manufacturers
Cathedral Stone
Products, Inc.
Hanover, Maryland
Tom Brown, Inc.
Phoenixville, Pennsylvania
Work on this project included demolition and construction for exterior restoration of the Marburg, Billings and Wilmer Buildings, which comprise the historic front façade of the Johns Hopkins Hospital. The John Shaw Billings Building is the signature of the campus and its dome is featured in the hospital’s logo and graphics.
The buildings are comprised of limestone and brick. Water infiltration and deterioration of the limestone and masonry prompted the repair project.
Site preparation included full scaffolding and shoring of the façade. It was constructed from grade level to the upper dome roof on all elevations.
A major challenge of the project was that the dome was composed of “Lime of Teil” block on the interior and certain portions of this were called to be removed and replaced. Original product to use for replacement was impossible to find due to age of the building which dates back to May 5, 1889.To rectify the problem, the contractor made molds and cast new “Lime of Teil” blocks for the dome from the restoration mortar.
Special features of this project are the reconstruction of the exterior dome finials. Also, the reconstruction of the ornamental limestone was extremely difficult and time consuming. The project included the limestone patches, as well as façade cleaning and finial panel exterior waterproofing.
Baldwin Reservoir Project
Award of Merit: Longevity Category
Baldwin Reservoir Project
Cleveland, Ohio
Submitted by Sika Corporation
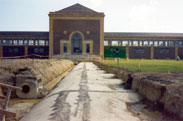
Owner
City of Cleveland Division
of Water
Cleveland, Ohio
Project Engineer/
Designer
City of Cleveland Division
of Water
Cleveland, Ohio
Material Supplier/
Manufacturer
Sika Corporation
Lyndhurst, New Jersey
The Baldwin Treated Water Reservoir was designed and constructed between 1918 and 1924 and placed in service in 1925. At 1035 ft long by 500 ft wide and 40 ft high from the floor to the crown of the groined arch roof, the twin underground basins make for one of the largest covered concrete reservoirs in the U.S.
The reservoir’s elegant arched roof was designed using the geometric character of the arch shape to support both the roof’s weight and the loads above it. This way, all vertical loads are transferred into compressive thrusts acting through the concrete arch roof. Since an arch functions primarily by transmitting forces through compression there are compressive stresses generated in the arch throughout the entire reservoir roof. The original designers cleverly utilized concrete’s compressive resistance ability to absorb and transmit the compressive force to the reservoir’s perimeter structural walls without reinforcing the entire roof structure. Standing safe and sound for the last 80 years, the Baldwin Reservoir helps provide high quality drinking water every day to Cleveland and surrounding suburbs.
In February 1993, after a routine inspection, the Water District was notified that a large quantity of potable water was found in a nearby storm drain. It was later confirmed that this water was leaking through cracks in the floor of Baldwin Reservoir. A complete investigation revealed a series of cracks in the non-reinforced concrete arched roof. The analysis indicated that the distress was due to seasonal thermal expansion and contraction of the roof structure.
Quadgraphics Floor Rehabilitation
Award of Merit: Longevity Category
Quadgraphics Floor Rehabilitation
West Allis, Wisconsin
Submitted by Degussa Building Systems
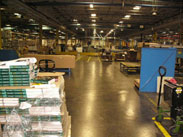
Owner
Johns Hopkins Hospital
Baltimore, Maryland
Project Engineer/
Designer
Kann & Associates
Baltimore, Maryland
Repair Contractor
Watts Restoration, Inc.
Croydon, Pennsylvania
Material Suppliers/
Manufacturers
Cathedral Stone
Products, Inc.
Hanover, Maryland
Tom Brown, Inc.
Phoenixville, Pennsylvania
A Korean War-era machine tool plant was closed and out of business. The State of Wisconsin had taken ownership of the abandoned facility. Jobs had been lost; the property taxes were off the City of West Allis’s books. What was to be done?
In 1994, QuadGraphics, of Pewaukee, Wisconsin, purchased the property and converted the old factory into a modern color printing and binding facility. The first step of conversion had to be the floors. This step was a big one; the 613,000 square ft of this more than 50 year-old facility had 8 in.-thick concrete floors surfaced with 2 1/4 in. thick, 3 x 5 in. wood block set in mastic. In addition, there were large pits where production machinery had operated since the 1950s.
The pits had to be filled, the wood block removed and the floor changed to a flat, non-dusting, wear resistant surface suitable for a modern high production printing plant. Inspection by the owner’s engineers found the floor was structurally sound. However, test cores taken from the floor revealed 40 years of machine tool production had left much of the concrete floor oil saturated.
Experienced concrete repair contractors know installation of bonded toppings can be chancy. Installing a bonded topping over an oil saturated concrete base would be a world-class challenge. The solution was a unique combination of surface preparation, chemical and mechanical bonding materials/methods, concrete design and logistical planning.
Eleven years later the floor is meeting the demands of twenty-four hours a day, seven days a week operation. Except for a few slightly worn joint areas, the floor has required no repair. The maintenance needs, just regular cleaning, have not changed since the floor was placed in service.
Seagull Beach Club
Award of Merit: Longevity Category
Seagull Beach Club
Cocoa Beach, Florida
Submitted by CPT of Florida, Inc.
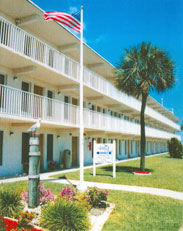
Owner
Seagull Beach Club
Cocoa Beach, Florida
Project Engineer/
Designer
Ben Mills & Associates
Palm Bay, Florida
Repair Contractor
Chematics of the South, Inc.
Cape Canaveral, Florida
Material Suppliers/
Manufacturers
CPT of Florida, Inc.
Cocoa Beach, Florida
Matcor, Inc.
Doylestown, Pennsylvania
The beachfront Seagull Beach Club, located in Cocoa Beach, Florida, is a three-story time-share condominium. In 1996, the concrete balconies (located on the north side) and walkways (located on the south side) showed signs of cracking, delamination, and spalling. The reinforcing steel required replaciement in part ,and in some areas it did not exist at all. Some of the balconies and walkways also had to be resloped to facilitate the drainage of rainwater.
In order to provide a long-term repair solution, the concept of cathodic protection and an impressed current conductive coating system was presented to and accepted by Seagull Beach Club. Much of the concrete had to be removed completely, forms installed, and replacement concrete poured.
The addition of an impressed current cathodic protection system (ICCP) was a pioneering decision by the board, since it was the first complete installation on a commercial building in the state of Florida. This decision proved to be a great investment for the owners since they are unlikely to ever have to pay for any concrete repair again, considering the extremely high chloride content in the concrete, and the age of the building (31 years old). The ICCP the system is now eight years old and will provide protection against future corrosion for another 20 years.
Atrium Palace Plaza Deck and Garage
Award of Merit: Transportation Category
Atrium Palace Plaza Deck and Garage
Fort Lee, New Jersey
Submitted by Structural Preservation Systems, Inc.
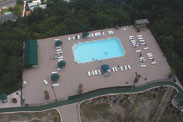
Owner
Atrium Palace Condominium Association
Fort Lee, New Jersey
Project Engineer/
Designer
O & S Associates
Englewood Cliffs, New Jersey
Repair Contractor
Structural Preservation Systems, Inc.
Hawthorne, New Jersey
Material Suppliers/
Manufacturers
American Hydrotech, Inc.
Chicago, Illinois
3M Concrete Protection Products
St. Paul, Minnesota
Constructed over 20 years ago, the Atrium Palace is a twenty-story condominium complex convenient to Manhattan. The Atrium offers health and fitness spas, a sauna, indoor/outdoor pools, tennis courts, and concierge services.
Surrounding the Atrium is a 153,200 square ft concrete plaza area sitting atop a two-level parking garage. The deck includes many amenities for the residents: tennis courts, a pool, basketball courts, a children’s play area, and a running track. Below the deck, the parking garage accommodates approximately 700 vehicles. Unfortunately, over time these areas suffered severe deterioration— mainly due to defects resulting from initial construction. In the garage, extensive shear cracking on the column corbels and beams was visible, as were spalls and failed post-tensioning tendons. On top of the garage, the deck was severely cracked, had failed expansion joints and was leaking water into the garage. Additionally, the recreational equipment was in poor condition and needed to be replaced. The appearance severely detracted from the elegance of the complex.
Restoring the structures to their intended use required intensive and well-coordinated repairs. Significant consideration had to be given to developing a complex phasing plan to ensure on-going facility operation. Each phase had to be designed and sequenced to displace only 150 parking slots at any one time. It is important to note that all work that had to be done in each area, above and below ground, had to be completed at the same time. Detailed scheduling was critical.
Through extensive planning, skilled execution, and communication with residents, this challenging project was a success. The owner was extremely satisfied with the results and is thrilled that the plaza and garage now enhance the atmosphere of the Atrium Palace.
6th Street Parking Garage Restoration
Award of Merit: Parking Structures Category
6th Street Parking Garage Restoration
Louisville, Kentucky
Submitted by Sika Corporation
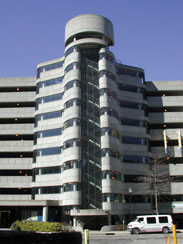
Owner
Parking Authority of
River City
Louisville, Kentucky
Project Engineer/
Designer
HNTB
Kansas City, Missouri
Repair Contractor
Schnell Contractors, Inc.
Louisville, Kentucky
Material Suppliers/
Manufacturer
Sika Corporation
Lyndhurst, New Jersey
Condition Analysis of Parking Garage Prior to Construction
Material Service Life Company
Monroeville, Pennsylvania
Monitoring Company of Corrosion Inhibitor Performance
C-Probe Technologies Ltd.
Lutterworth, United Kingdom
The 6th and Main Street Parking Garage, built in 1987 with a south bay addition in 1990, is a nine-level,cast-in-place, post-tensioned structure began showing signs of severe distress. A structural analysis showed the cause of the spalling to be the result of high chloride content at the level of reinforcing. Many areas that were previously repaired remained intact, but other spalls had also developed. The future appeared to be an ongoing battle against corrosion, knowing that high chloride levels were already present in the concrete but had not yet penetrated the steel reinforcement depth. The condition analysis offered a unique perspective on understanding and controlling the corrosion. Future prediction models allowed the owner to choose the repair strategy with an estimated benefit in terms of service life.
Restoration materials and methods included the use of bonding agents, repair mortars, joint sealants and membranes, corrosion inhibitors, sealers, and traffic deck membrane technologies. Because the use of an anodic and cathodic mixed corrosion inhibitor offered an excellent cost-to-benefit ratio, a measurement tool was required to understand its effectiveness. Knowledge of the corrosion inhibitor’s past performance was readily available through the manufacturer’s test results and various projects and field trials, but understanding the corrosion activity was very important. What will the corrosion activity look like after the corrosion inhibitor is applied, after six months, a year, two years, and further down the life of the structure? A state-of-the-art monitoring program would show the results of the corrosion inhibitor over a 2 year period by testing programs in 6 month intervals.
Strengthening of Tubular Centrifuged Posts
Award of Merit: Special Projects Category
Strengthening of Tubular Centrifuged Posts
Sao Paulo, Brazil
Submitted by Degussa Construction Chemicals Latin America
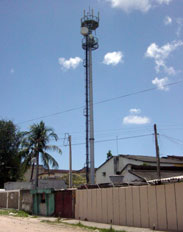
Owner
Telesp Celular (VIVO)
Sao Paulo, Brazil
Project Engineer/
Designer
Paula Machado Engenharia de Projectos
Belo Horizonte, Brazil
Repair Contractor
PhDesign Concreto, Construcao e Reabilitacao Ltd.
Sao Paulo, Brazil
Material Suppliers/
Manufacturer
Degussa Construction Chemicals Brazil
Sao Paulo, Brazil
The main objective of this repair project was to strengthen reinforced concrete poles. This project was necessary to correct the original design deficiencies that caused a total of eight collapsed concrete telephone poles to date in Brazil. In each of the known collapses, the failure occurred within the development length between the first module (fixed to the ground) and the second module.
Before the companies involved in the project—the repair contractor and the project engineer—learned about this predicament, several posts were removed and replaced by metallic towers. After investigation, the aforementioned team decided to present the owners with an alternative approach: the carbon fiber-reinforced polymer (CFRP) concept, as an ideal solution for their particular case.
The structural solution employed, which was used on 150 poles, was to apply an average of 540 square ft (50 square m) of CFRP system to each pole to be repaired. The heights of these concrete poles varied incrementally from 60 to 197 ft (20 to 60 m).
On average, the rehabilitation cost is approximately 1/3 of the value of the removal and replacement of the post by a metallic tower. This provides an attractive option for the companies in this business both in time and repair costs. It also provides a solution to the design of any additional new concrete poles to be installed in the future, instead of losing the market to metal poles.
Structural Restoration of Florida's Gulfarium
Award of Merit: Special Projects Category
Structural Restoration of Florida's Gulfarium
Fort Walton Beach, Florida
Submitted by Phoenix Coatings, Inc.
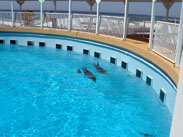
Owner
Gulf Exhibition Corporation
Fort Walton Beach, Florida
Project Engineer/
Designer
John R. Oglesby, PE
Pensacola, Florida
Repair Contractor
Phoenix Coatings, Inc.
Pensacola, Florida
Material Suppliers/
Manufacturer
Sika Corporation
Lyndhurst, New Jersey
Florida’s Gulfarium is the oldest marine show aquarium in the world. Its ability to remain in operation came into question when, in late 2004, the Gulfarium requested an inspection for corrosion of the steel dolphin tank and the surrounding concrete structure. The steel tank was in desperate need of cleaning and a new coating system, and the concrete structure was found to be severely deteriorated. The Gulfarium’s location (directly on the Gulf of Mexico) was the reason for its structural deficiencies. The Gulf’s chloride-ion-infused water had infiltrated the concrete, attacking the steel.
The restoration contract required a substantial completion date of March 31, 2005, but the pregnancies of two of the performing dolphins necessitated completion by March 3, 2005. This presented a dilemma—structural repairs were essential, as was returning the dolphins to their main tank in time for tourist season. The restoration team collaborated to establish a plan to achieve restoration of the facility and meet the deadline.
To avoid further structural deficiencies, the concrete was recast using 5000 psi (34 MPa) concrete with a corrosion inhibiting admixture incorporated into the design mixture. Changes to the original design of the structure also included the addition of expansion joints, sealing systems, reinforcing steel, and decorative waterproof coatings.
The dolphins were returned to their tank just in time, thanks to the hard work, quick thinking, and detailed planning of the project team. The contractor left the owner with a solid plan for completing the remainder of the restoration during the following “off season.” Everyone involved was satisfied with a quality restoration project.
Rehabilitation of Dao Kanong Bridge
Award of Merit: Transportation Category
Rehabilitation of Dao Kanong Bridge
Bangkok, Thailand
Submitted by IETL Co., Ltd.
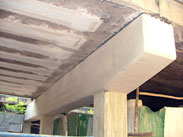
Owner
Department of Public Works, BMA
Bangkok, Thailand
Project Engineer/
Designer
IETL Co., Ltd.
Bangkok, Thailand
Repair Contractor
IETL Co., Ltd.
Bangkok, Thailand
Material Suppliers/
Manufacturers
Degussa Construction Chemicals
Bangkok, Thailand
Nontri Company, Ltd.
Bangkok, Thailand
The Dao Kanong Bridge, a 30-year-old reinforced concrete two-lane bridge with 21 spans, is located on Ratcha Burana Road in western Bangkok. The bridge was found to have an insufficient safety index (Bangkok Metropolitant Administration’s highway standard) due to serious structural deterioration and heavy traffic load. Damage and deterioration from corrosion and separation of prestressed concrete planks could lead to abrupt failure of bridge decks, as it occurred to some bridges in Bangkok in the past.
The rehabilitation procedures had to be done within a limited time frame without disturbing traffic, both trucks and barges. The bridge could only be closed one lane at a time, and only for a few hours late at night, because this bridge is on one of the main truck routes in Bangkok.
Due to the unavailability of structural drawings and other important structural information, many nondestructive test (NDT) were carried out to evaluate existing conditions. Load tests were applied before, during, and after strengthening procedures to study structural behaviors and to evaluate strength and safety conditions.
Carbon fiber composites had been selected for substitution of corroded reinforcement and for strengthening main structural members. After all rehabilitation procedures were completed, the final load test confirmed ability of the bridge to carry the required service load level safely.